Sealing is a critical factor for many industries, especially in the energy, transportation, and health sectors. To meet these demanding requirements, elastomers stand out due to their unique properties. They provide effective sealing against liquids, powders, and more, even in harsh environments. Whether for submerged equipment or devices exposed to high-pressure and high-temperature conditions, elastomers prove to be a reliable and durable solution.
Case study: rubber
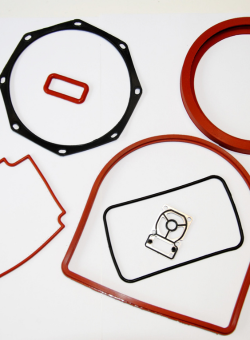
Flexible, thermally resistant, and able to retain its properties under mechanical stress, rubber is a preferred choice for various applications, including sealing.
Our FKM rubber (or Viton) offers exceptional tolerance to high temperatures, along with excellent resistance to oils, hydrocarbons and chemicals. This material is a fluoroelastomer compliant with REACH and POP (EU 2019/2021) regulations. Its specific formulation makes it ideal for demanding industrial environments, such as filtration systems for complex or corrosive liquids. FKM rubber is widely used in the automotive industry, where we supply compressor seals, head gaskets, and membranes.
We offer a wide range of FKM rubbers, suitable for compression or injection molding processes, capable of producing parts ranging from 0.50 grams to several kilograms, with hardness between 50 and 90 ShA.
Case study: silicone
To meet the most demanding sealing requirements, we also provide a selection of silicones with specific characteristics.
Designed for the transportation sector and compliant with EN 45545-2, Stirmotiv® silicone offers excellent electrical insulation, high thermal stability, and fire resistance. The smoke released in the event of a fire is non-toxic. These properties make it suitable for air conditioning seals, electrical insulators, or lighting seals, among other applications.
For dynamic applications requiring perfect sealing, such as liquid transfer, we recommend Hightube®, a high-performance tube particularly suited for peristaltic applications. It meets CE 1935/2004 MG0, European Pharmacopoeia 3.1.9, FDA 21 CFR 177.2600, ISO 10993 (parts 5, 6, and 11), REACH, USP Class VI, and XV BfR "Silicones" standards.
Our Staminalene® silicone is renowned for its exceptional resistance to abrasion, fatigue, and mechanical stresses (torsion, bending, compression). Compliant with FDA, RoHS, REACH, ISO 10993, and USP Class VI standards, it is used for sealing applications such as autoclave or valve seals, inflatable seals, and fluid transfers.
For applications requiring increased resistance to extreme temperatures, such as O-rings or oven seals, our Stirlene® silicone is perfectly suited.
StilUVene, a silicone compliant with XV BfR "Silicones”, FDA 21 CFR 177.2600, USP Class VI, and ISO 10993 (parts 5, 6, 10, and 11), combines high thermal stability and flexibility at low temperatures with a long lifespan under dynamic stress. It is especially suitable for overmolding and coextrusion of heat-sensitive materials since its curing temperatures are lower than those of HTV (High Temperature Vulcanization) silicones.
Whether for static or dynamic sealing solutions, our inflatable seals are designed to compensate for pressure differences and/or temperature variations between interior and exterior environments. They also fill large gaps, providing an effective barrier between enclosure deltas and its surroundings.
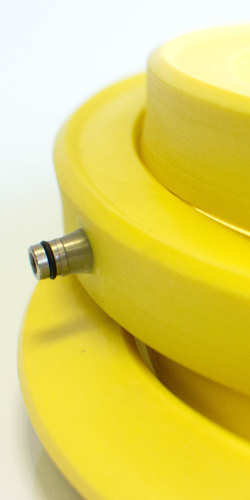
Case study: polyurethane
Polyurethane stands out for its durability, high resistance to abrasion and impact, dynamic stress, and its resistance to oils and hydrocarbons. These exceptional properties make this elastomer particularly suitable for harsh environments where sealing is essential.
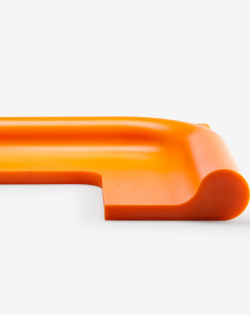
Our UREFLEX® range of polyurethanes, compliant with RoHS and REACH standards, offers versatile and durable sealing solutions for various industries. For instance, it can be used in the hydroelectric sector, where it is employed for bearings and seals subject to intense wear. Our polyurethanes are also used in the subsea sector, notably for J-Tube Seals, where the inner surface is often difficult to protect with conventional anti-corrosion systems. A sealing device must be installed at the bottom of the tube to ensure sealing between the J-Tube Seal and the umbilical tube. That's why we manufacture UREFLEX® TM370 seals, providing an effective anti-corrosion solution and ensuring long-lasting protection.
Moreover, our UREFLEX® A, R, TM, and U Moca Free polyurethanes comply with EDF's technical note on limited chemical species (PMUC – D309515012254, ind A), making them suitable for sealing solutions in nuclear plants. Additionally, we offer solutions for food contact (CE 1935/2004 and EU 10/2011), specifically designed to resist hydrolysis and wet abrasion. Our UREFLEX® TM390 is ACS certified, making it safe for contact with drinking water.
Thanks to their flexibility and strength, elastomers ensure optimal sealing while extending the lifespan of the systems in which they are integrated.